Unlocking The Potential Of Your Mechanical/Electrical Room
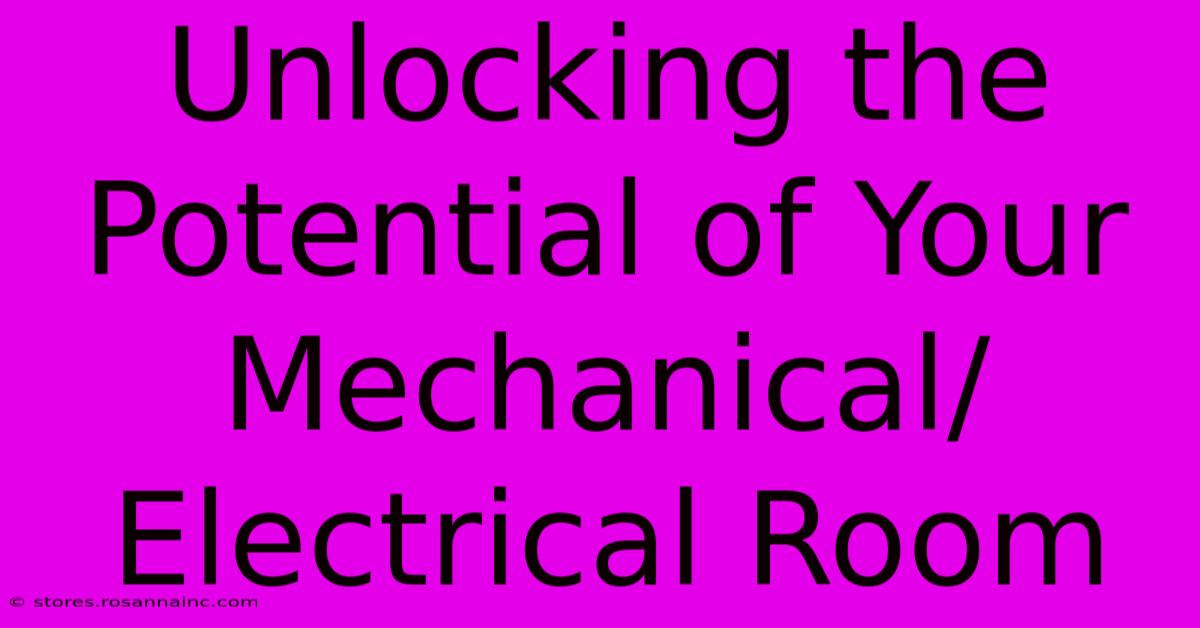
Table of Contents
Unlocking the Potential of Your Mechanical/Electrical Room
Your mechanical/electrical (M/E) room – often overlooked and tucked away – is the beating heart of your building. It houses the critical systems that ensure comfort, safety, and operational efficiency. But are you truly maximizing its potential? A well-maintained and strategically designed M/E room isn't just about avoiding costly breakdowns; it's about optimizing performance, enhancing energy efficiency, and extending the lifespan of your equipment. This comprehensive guide will explore how to unlock the full potential of your M/E room.
Understanding Your M/E Room's Importance
Before diving into optimization strategies, let's reiterate the critical role your M/E room plays:
- HVAC Systems: These systems control heating, ventilation, and air conditioning, directly impacting occupant comfort and productivity. A poorly managed M/E room can lead to inconsistent temperatures, poor air quality, and increased energy consumption.
- Electrical Distribution: This includes power panels, transformers, and other equipment responsible for delivering electricity throughout the building. Effective management prevents power outages and ensures consistent electrical supply.
- Plumbing and Fire Protection: Your M/E room may house crucial components of your building's plumbing and fire suppression systems, critical for safety and operational continuity.
- Building Automation Systems (BAS): Many modern buildings use BAS to monitor and control various systems, often managed from the M/E room. Optimizing this system can significantly enhance efficiency.
Key Strategies for Optimizing Your M/E Room
Optimizing your M/E room requires a multi-pronged approach encompassing preventative maintenance, strategic design, and technological advancements.
1. Preventative Maintenance: The Cornerstone of Efficiency
Regular preventative maintenance is paramount. A proactive approach significantly reduces the risk of unexpected breakdowns and costly repairs. This includes:
- Scheduled Inspections: Implement a rigorous schedule for inspecting all equipment, checking for wear and tear, loose connections, and potential issues.
- Cleaning and Debris Removal: Dust and debris accumulation can impair equipment performance and create fire hazards. Regular cleaning is essential.
- Filter Replacement: Replacing air filters in HVAC systems regularly ensures optimal airflow and prevents the buildup of contaminants.
- Calibration and Testing: Regularly calibrate and test sensors, controllers, and other critical components to maintain accuracy and reliability.
2. Strategic Design and Organization: Maximizing Space and Accessibility
The layout and organization of your M/E room directly impact efficiency and safety:
- Clear Aisles and Pathways: Ensure adequate space for easy access to all equipment for maintenance and repairs. This minimizes downtime and improves safety.
- Organized Wiring and Piping: Neatly organized wiring and piping prevent confusion and improve safety, reducing the risk of accidental damage. Proper labeling is crucial.
- Adequate Ventilation: Ensure proper ventilation to prevent overheating and maintain a safe working environment.
- Emergency Lighting and Shut-off Switches: Clearly mark emergency exits, lighting, and shut-off switches for safety.
3. Embracing Technology for Enhanced Efficiency
Technology plays a significant role in optimizing your M/E room:
- Building Automation Systems (BAS): A well-configured BAS allows for remote monitoring, control, and data analysis of your building's systems, leading to significant energy savings.
- Predictive Maintenance: Utilizing sensor data and machine learning, predictive maintenance can anticipate potential failures, allowing for proactive repairs and minimizing downtime.
- Energy Monitoring Systems: These systems track energy consumption, identifying areas for improvement and reducing overall energy costs.
4. Regular Training for Personnel
Ensure your personnel are properly trained on the operation and maintenance of all equipment within the M/E room. This reduces the risk of errors and improves overall efficiency. Regular training updates are essential to keep staff current on new technologies and best practices.
The Bottom Line: A Well-Managed M/E Room Equals Significant Returns
Investing in the optimization of your mechanical/electrical room is not merely an expense; it's a strategic investment that yields significant returns in the form of:
- Reduced Energy Costs: Improved efficiency translates to lower energy bills.
- Extended Equipment Lifespan: Preventative maintenance and proactive management extend the life of your equipment, delaying costly replacements.
- Improved Building Safety: A well-maintained M/E room contributes to a safer working environment.
- Enhanced Occupant Comfort: Efficient HVAC systems ensure a comfortable and productive environment for building occupants.
- Reduced Downtime: Preventative maintenance and efficient management minimize interruptions to building operations.
By implementing these strategies, you can unlock the full potential of your M/E room, contributing to a more efficient, safer, and more comfortable building for everyone. Remember, a proactive approach to maintenance and optimization is key to achieving long-term success.
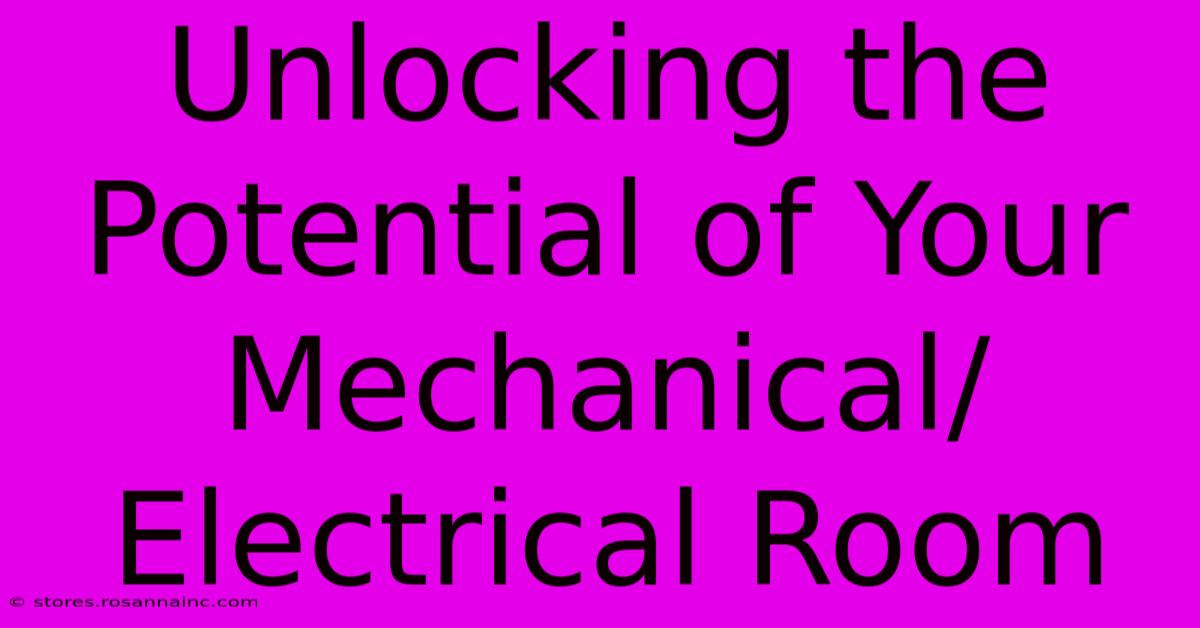
Thank you for visiting our website wich cover about Unlocking The Potential Of Your Mechanical/Electrical Room. We hope the information provided has been useful to you. Feel free to contact us if you have any questions or need further assistance. See you next time and dont miss to bookmark.
Featured Posts
-
Data Duel Uncovering Hidden Uruguay Brazil Trends
Feb 09, 2025
-
Capital Murder Definition Everything You Need To Know In One Place
Feb 09, 2025
-
Romano Reveals Eye Injury
Feb 09, 2025
-
Where Are They Now The Spy Kids 2 Cast All Grown Up
Feb 09, 2025
-
Mission San Jose California History Beauty And Community
Feb 09, 2025